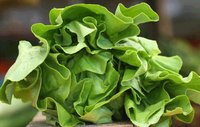
Polyethylene Covering with Boiler Heating
Some greenhouses are covered in glazed glass. Ours is a more economical model. It is a polyethylene-covered Quonset-type structure, one hundred feet by thirty feet, giving us 3,000 square feet of workspace underneath.
Since a single layer of polyethylene would not protect our hydroponically-grown lettuce from the vagaries of the outside temperature, we’ve used two layers of plastic to cover the structure, then forced air between the two layers to create a four to six inch airspace. This is an excellent insulating barrier; with the onset of winter fast approaching, that is an important consideration.
In the plastic area, several other possible coverings had to be considered. We could have covered our greenhouse with acrylic sheets, polycarbonate plastic, or fibreglass. Polyethylene won out, largely because it is the most cost-effective.
With nighttime temperatures increasingly dropping below freezing, once again we’ve become very aware of how we chose to heat our greenhouse. First, we had to figure out what the anticipated coldest temperature was that we had to deal with, while maintaining an even 68º F (20º C), which is the optimum indoor level for our plants to thrive.
After poring through data going back many years, we found that it rarely dropped below 23º F (-5º C) in our neck of the woods. Most of the time during winter, the thermometer hovered around the freezing point. So we had to purchase a system that could easily deal with such temperature drops, and the occasional dip below the norm.
By a complicated set of calculations involving exchange, conductive, and radiation heat loss, as well as a heat loss coefficient, we arrived at the conclusion that at an outside temperature of 23º F we would need to generate 1,484,861 British Thermal Units per hour (Btu’s) with whatever system we installed.
Of course, our system of 45—600W High Pressure Sodium lights also generates quite a few BTU’s per hour, so that heat had to be factored in.
In addition, we not only had to heat the circulating air around the lettuce, but also the Nutrient Pond, which is their growing medium. Given that many growers urged us to buy a central Boiler and use Hot Water Heating throughout the greenhouse, that’s what we did.
Even though the initial cost outlay was more than using a number of space heaters or forced air ones, the convenience of running hot water pipes underneath the surface of our growing medium, convinced us that this was the way to go.
We chose finned-tube convectors around the walls of the greenhouse, as opposed to straight steel pipes, since they provide four to five times the heat transfer capacity of bare pipe. They’re harder to keep clean, but much more efficient, reducing our heating bill.
In light of the mishap that happened last week, we’re grateful to have a central Boiler system, since in the case of power failure, the water stays hot for a couple of hours, until an alternate source of power can be hooked up.
After the HyOx flush, we administered not only Piranha, Tarantula, and Voodoo Juice, but also SensiZym, Sensi Cal Mg. Mix Grow, and a new batch of our primary nutrients, Micro and Grow.
Our lettuce are well taken care of, and that includes keeping them warm in the winter, and cool in the summer. A number of fans help to circulate the air above our Nutrient Pond, so that no pockets of hot or cold air can damage the sensitive leaves of our lettuce plants.
posted by silvio @ 9:19 PM
0 comments
0 Comments:
Post a Comment
<< Home